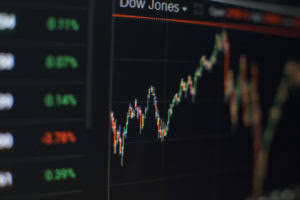
Accurately tracking these costs ensures your calculations reflect the actual cost of labor. At each step, a different production cost adds up, giving you a complete picture in the form of COGM. But it’s a step-by-step process, and you need practical actions to reach precise COGM confidently. Once you accurately calculate the cost of goods manufactured (COGM), you can make informed decisions about pricing, budgeting, and overall financial planning. Reducing Insurance Accounting labor costs is an excellent way to lower the expense of goods manufactured without compromising product quality.
Cost of Goods Manufactured (COGM)
Total manufacturing cost (TMC), also called total cost of production, is the all-in number for what it takes to make goods during a specific period. It covers everything tied to production–raw materials, labor, and factory overhead. Cost of Goods Manufactured (COGM) is a common accounting term used in managerial accounting.
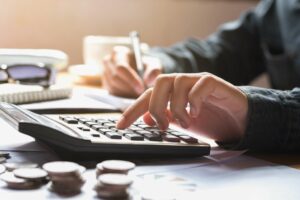
An Example of Cost of Goods Manufactured (COGM) Calculation in Action
Without understanding COGM, you’re essentially flying blind when it comes to pricing, profitability, and inventory management. In this article, we’ll break down everything you need to know about calculating COGM, step by step. By the end, you’ll have a clear roadmap to mastering this crucial aspect of production accounting. Note how the statement shows the costs incurredfor direct materials, direct labor, and manufacturing overhead. Thestatement totals these three costs for total manufacturing costduring the period.
Manufacturing Overheads Calculation
The technology not only speeds up payroll processing but also allows you to manage all other activities such as overtime, benefits, bonuses, training programs, and much more. Deskera Books enables you to manage your accounts and finances more effectively. Maintain sound accounting practices by automating accounting operations such as billing, invoicing, and payment processing. If we incorporate those inputs into our WIP model, the cost of manufactured products comes to $25 million (COGM). The initial WIP inventory amount for 2021 will be $20 million and will be based on the ending WIP inventory balance from 2020.
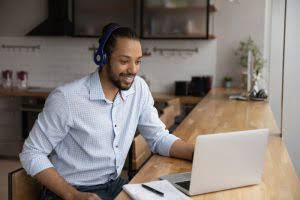
What are indirect materials in COGM?
Review production processes, reduce waste, negotiate better rates with suppliers, and leverage automation tools like ERP software. While both focus on production-related costs, they serve different purposes and include distinct components. Work-in-process (WIP) inventory calculations can often cause errors, but Kladana eliminates this issue by automating the tracking and adjustment process. This amount highlights the wages that Company A paid to employees directly involved in the production process. The tips below should help you prepare an accurate and actionable schedule.
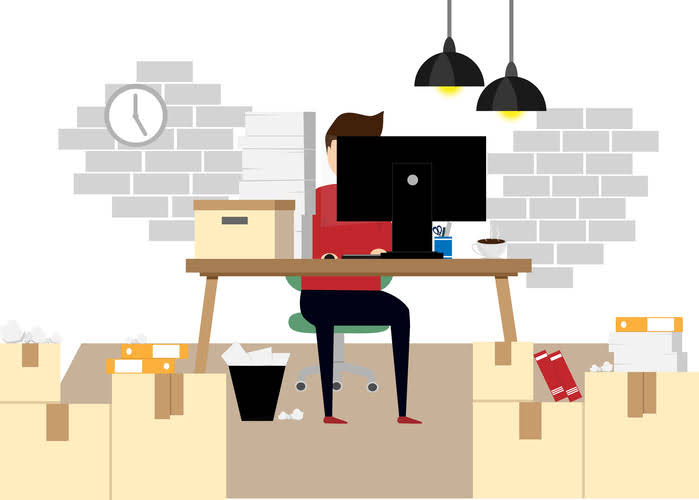
- Well for starters, it changes everything about the way you need to report your end of year revenue and expenses to the IRS.
- As a maker, one of the first things to realise is that you are not just a retailer of your goods – you are also a manufacturer of them.
- It’s compatible with Zebra and Honeywell barcode scanners, making it easy to track raw materials in real-time.
- COGM is good for analyzing your internal manufacturing processes and supply chains, whereas COGS is more beneficial in reporting your internal manufacturing expenses against your revenue.
This vital information, if properly implemented, will help the company improve the production of goods manufactured. So while COGM is not reported on the income statement, it is used to calculate COGS, which is included in the income statement. Direct materials, such as steel used to construct automobile frames or fabric in clothing manufacturing, may be easily linked to a particular product or unit of production.
Cost of Goods Manufactured Formula
- Now that you’ve calculated direct materials, direct labor, and manufacturing overhead, it’s time to add them all together to determine your total manufacturing costs.
- Synder’s product mapping feature matches and tracks items seamlessly, even if you have different product names across platforms, you can still track them as one product.
- Finding this variable is easy because most organizations keep time logs for their workers.
- This adjustment accounts for the change in the value of goods that are still in the production process and still need to be completed.
- This automation ensures your calculations are consistent and free from human errors.
- If you’re running a manufacturing business, you’ve probably heard the term “Cost of Goods Manufactured” or COGM.
Every product tells a story–not just of design and delivery but of the costs and decisions that bring it to life. For businesses, understanding the cost of goods manufactured (COGM) isn’t just about crunching numbers; it’s about uncovering the real drivers behind profitability and efficiency. From tracking production expenses to setting competitive prices, COGM holds the key to staying in control of your operations. The COGS refers to the total money a company spends on labor, materials, and overhead costs related to its cogm production processes or services.
During his time working in investment banking, tech startups, and industry-leading companies he gained extensive knowledge in using different software tools to optimize accounting business processes. The concept of lean manufacturing is all about reducing waste to an absolute minimum. According to lean manufacturing principles, there are seven types of waste that a company should address to be efficient.